Lithium-ion battery
The metals contained in electronic waste, especially precious metals, have a grade that is tens or even hundreds of times higher than natural mineral deposits, and the recovery cost is generally lower than mining natural mineral deposits. The multiple hearth furnace (MHF) pyrolysis technology separates and recovers these precious metals, while also reducing harmful emissions associated with traditional precious metal recovery. The final product is a homogeneous concentrate of precious metals, with a grade typically higher than that of traditional mining concentrates. Not to seize market share from existing recyclers, but to focus on obtaining materials from dump and landfills, which belong to the low-end of the value range of electronic waste.

-
Compliance with regulations - continuous monitoring to ensure pollution-free emissions .
-
Power generation - waste heat is recovered to provide power for operation, and the remaining electricity is reintroduced into the local power grid.
-
100% recovery - The grade of the final product is usually higher than that of traditional mining concentrates, and 100% recovery.
-
Safe and easy to smelt and transport - Concentrates are processed safely with fewer logistics and border control restrictions.
Company is committed to environmental protection and environmental engineering industry, the technology research and development team of the international advanced technology digestion and re-innovation, cooperation with domestic and foreign equipment manufacturers, the formation of its own core equipment- MHF. MHF is used in the electronic waste pyrolysis and recycling, sludge pyrolysis and incineration, comprehensive utilization of biomass resources, mineral roasting, activated carbon carbonization/activation, activated carbon regeneration, activated carbon application (biological fermentation product decolorization/ wastewater treatment, etc.) and other fields, master more than 30 corresponding patents, more than 80 sets of MHF engineering experience.
The waste lithium battery recycling project aims to develop new processes for the recycling of retired lithium batteries, improve the recycling rate of key materials, reduce technical costs, and provide a reliable process route for the resource recycling of key materials in lithium batteries. The dry process for recycling waste lithium batteries and metal waste can make up for the shortcomings of the domestic battery recycling and reuse industry chain, with a high matching degree with production capacity, obvious comprehensive cost advantages, and a development direction that meets the needs of mainstream customers.
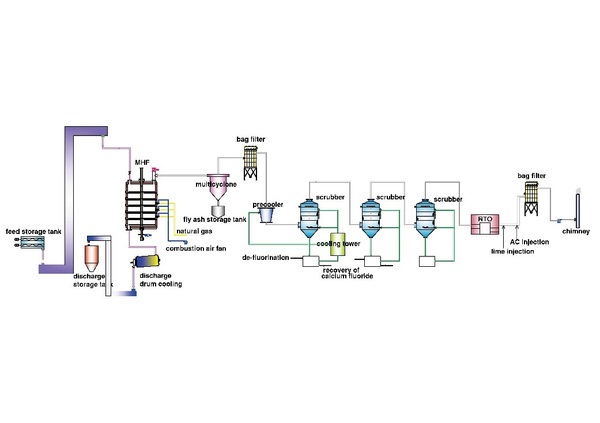
The pyrolysis process consists of three stages
Self-heating volatilization section: 200-300 ℃. The moisture separates from the material in the form of steam, and the organic solvent begins to evaporate. The binder is heated and still adheres to the metal black powder. During the material falling process, it is stirred layer by layer by the rake teeth, and undergoes sufficient heat exchange with the rising hot flue gas. The heat consumed in this stage is the heat contained in the hot flue gas generated by pyrolysis and carbonization, which belongs to the self-heating stage.
Pyrolysis carbonization section: 400-550 ℃. As the bottom temperature rises, PVDF and CMC binders begin to peel off the black powder, decompose and volatilize, and produce a mixture of gases such as CO and CH4 under anaerobic conditions; The heat generated by incomplete combustion of organic matter after volatilization is released in the furnace, reducing the consumption of natural gas.
Natural cooling section: A cooling layer is installed at the bottom of the furnace, and the carbonized black powder naturally cools down in the furnace to avoid spontaneous combustion. At the same time, the high-temperature heat is carried away by the countercurrent cooling wind, which is used to dry and carbonize the upper layer of raw materials.
Advantages of multi chamber furnace lithium battery pyrolysis and recovery:
-
Vertical structure, compact system with small footprint, continuous operation for 7 * 24 hours.
-
Internally heated oxygen content<1%, reduces greenhouse gas formation and emissions, self-heating drying, high waste heat utilization rate, and low heat demand.
-
Each layer is equipped with soft stirring control, allowing the material to fully contact and react with hot flue gas.
-
Accurate control of temperature stratification during operation, fully removing moisture, organic matter, PVDF binder, etc., to obtain high-grade target products.
-
The system operates automatically, and the entire process of feeding, disposal, and discharging is enclosed, with less manual demand.

Waste lithium battery pyrolysis project

Zhejiang University waste lithium battery pyrolysis pilot test

Baosteel Shaoguan waste lithium battery pyrolysis pilot test